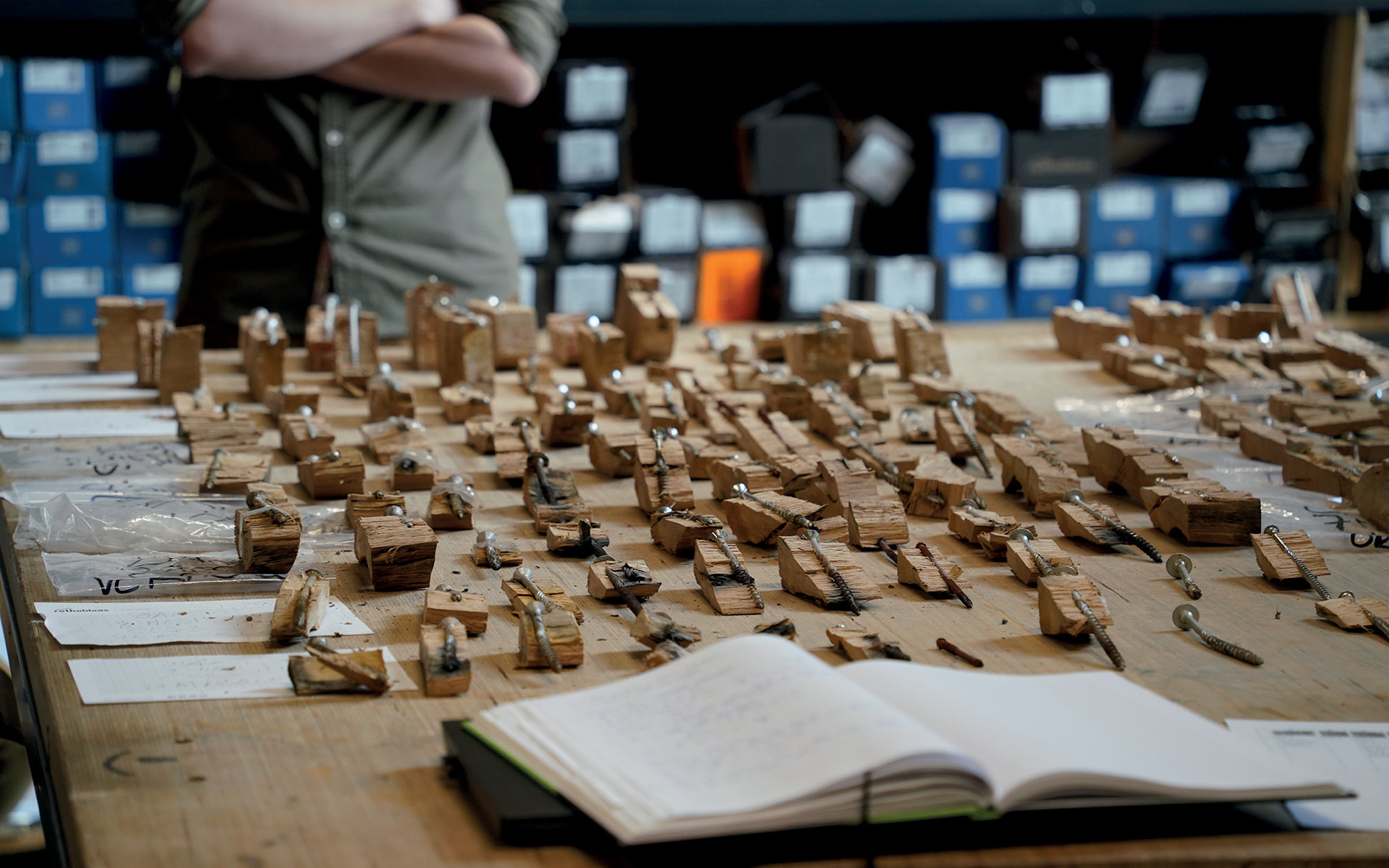
Holzbauschrauben: Ein Leitfaden zu den Risikofaktoren
Bei der Planung oder Fertigung von Holzbauten kann die Wahl der Schrauben den Unterschied zwischen einem Element mit jahrzehntelanger Lebensdauer oder aber mit schneller Qualitätsminderung bedeuten. Feuchtigkeit, Chloride, Luftverschmutzung und sogar die chemische Zusammensetzung des Holzes selbst sind Variablen, die die Korrosionsanfälligkeit von Schrauben bestimmen. Wenn diese Variablen vernachlässigt werden, können die Gesamtstabilität eines Bauwerks beeinträchtigt und die Wartungskosten deutlich erhöht werden.
Holzbauschrauben stehen in direktem Kontakt mit chemischen und Umwelteinflüssen. Wenn diese besonders aggressiv sind, können sie bereits nach wenigen Wochen sichtbare Korrosionsprozesse auslösen. Es ist daher wichtig, die Nutzungsklassen (welche die thermohygrometrischen Betriebsbedingungen beschreiben) und die Korrosivitätskategorien (atmosphärische Umgebungen und Holz) zu kennen, um die am besten geeigneten Baustoffe und Verkleidungen zu wählen.
Nachfolgend finden Sie einen Überblick über die wesentlichen Risikofaktoren sowie Angaben zu den gängigsten Holzarten und Stählen, auf deren Grundlage Sie sich für die richtigen Holzbauschrauben entscheiden können.
Korrosion in Holzbauschrauben: Informationen zum Phänomen und seinem Auftreten
Korrosion ist ein Zersetzungsprozess von Metall. Er tritt auf, wenn die Metalle, aus denen die Schrauben gefertigt sind, mit Feuchtigkeit und Chemikalien in der Umgebung oder im Holz reagieren. Die wichtigsten Faktoren, die eine Korrosion beschleunigen, sind:
Relative Feuchtigkeit: Je feuchter die Umgebung, desto schneller der Korrosionsprozess
Chloride: Sie sind typisch für Küstengebiete oder Gebiete, in denen Tausalze verwendet werden, und begünstigen lokalisierte Korrosionsprozesse.
Atmosphärische Schadstoffe: Stoffe wie Schwefeldioxid und Stickoxide, die in Umgebungen mit starker Urbanisierung, wie beispielsweise Megacitys, oder in der Nähe von Schwerindustrie vorkommen, können eine Korrosion erheblich beschleunigen.
Chemische Eigenschaften von Holz: Ein saurer pH-Wert oder chemische bzw. Wärmebehandlungen (z. B. auf Kupferbasis oder mit Flammschutzmitteln) beeinflussen die Oxidation der Schrauben erheblich.
Wird lediglich berücksichtigt, was mit dem freiliegenden Teil des Metalls geschieht, ohne darauf zu achten, was im Inneren des Holzes passiert (und umgekehrt), kann es zu unzureichenden und riskanten Beurteilungen kommen. Deshalb muss vor der Auswahl von Holzbauschrauben klar sein, in welcher Umgebung und auf welchem Untergrund sie montiert werden.
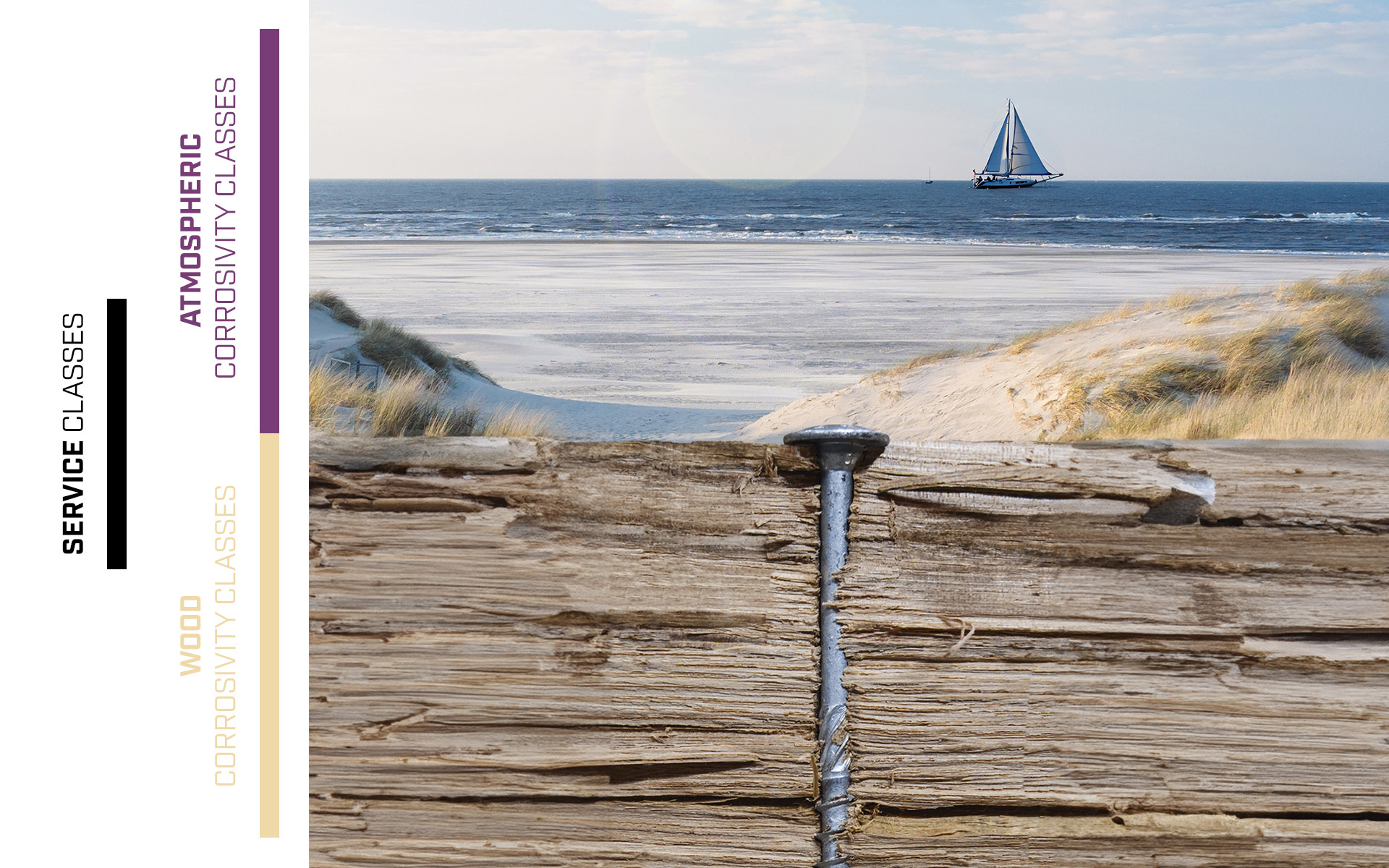
Nutzungsklassen und Korrosivitätskategorien: atmosphärische Umgebungen und Holz
Die Bezugsnorm (EN 14592:2022) unterteilt die Expositionsbedingungen in Nutzungsklassen und Korrosivitätskategorien, um Planern und Herstellern die Auswahl zu erleichtern.
Nutzungsklassen
Die Nutzungsklassen (SC1, SC2, SC3, SC4) beschreiben den Feuchtigkeitsgehalt des Holzes abhängig von den thermohygrometrischen Umgebungsbedingungen:
SC1: Elemente in Innenräumen mit niedrigen und relativ stabilen Feuchtigkeitswerten. Die Feuchtigkeitsschwankungen sind minimal.
SC2: Elemente in teilweise überdachten Bereichen oder mit mäßiger Luftfeuchtigkeit. Dies sind nicht vollständig isolierte Veranden oder Dächer, bei denen das Holz gelegentlich Feuchtigkeit aufnehmen kann.
SC3: Elemente, die Witterungseinflüssen ausgesetzt sind oder sich in Umgebungen mit starker Feuchtigkeit befinden. Die thermohygrometrischen Schwankungen sind groß, und der Wassergehalt des Holzes erreicht hohe Werte.
Die US-amerikanischen (NDS) und kanadischen Vorschriften (CSA:O86) definieren auf ähnliche Weise Bedingungen für eine Feuchtigkeitseinwirkung, die mit der Nutzungsklasse vergleichbar sind:
DRY-Bedingungen: entspricht SC1 und SC2 mit Feuchtigkeitsanteilen von bis zu 19 %.
WET-Bedingungen: entspricht den Klassen SC3 und SC4 mit Feuchtigkeitswerten über 19 %.
Die Kenntnis der Nutzungsklasse hilft abzuschätzen, wie stark sich das Holz im Laufe der Zeit mit Wasser vollsaugt. Je höher der Feuchtigkeitsgehalt des Werkstoffs, desto stärker sind die Holzbauschrauben einem korrosiven Angriff ausgesetzt.
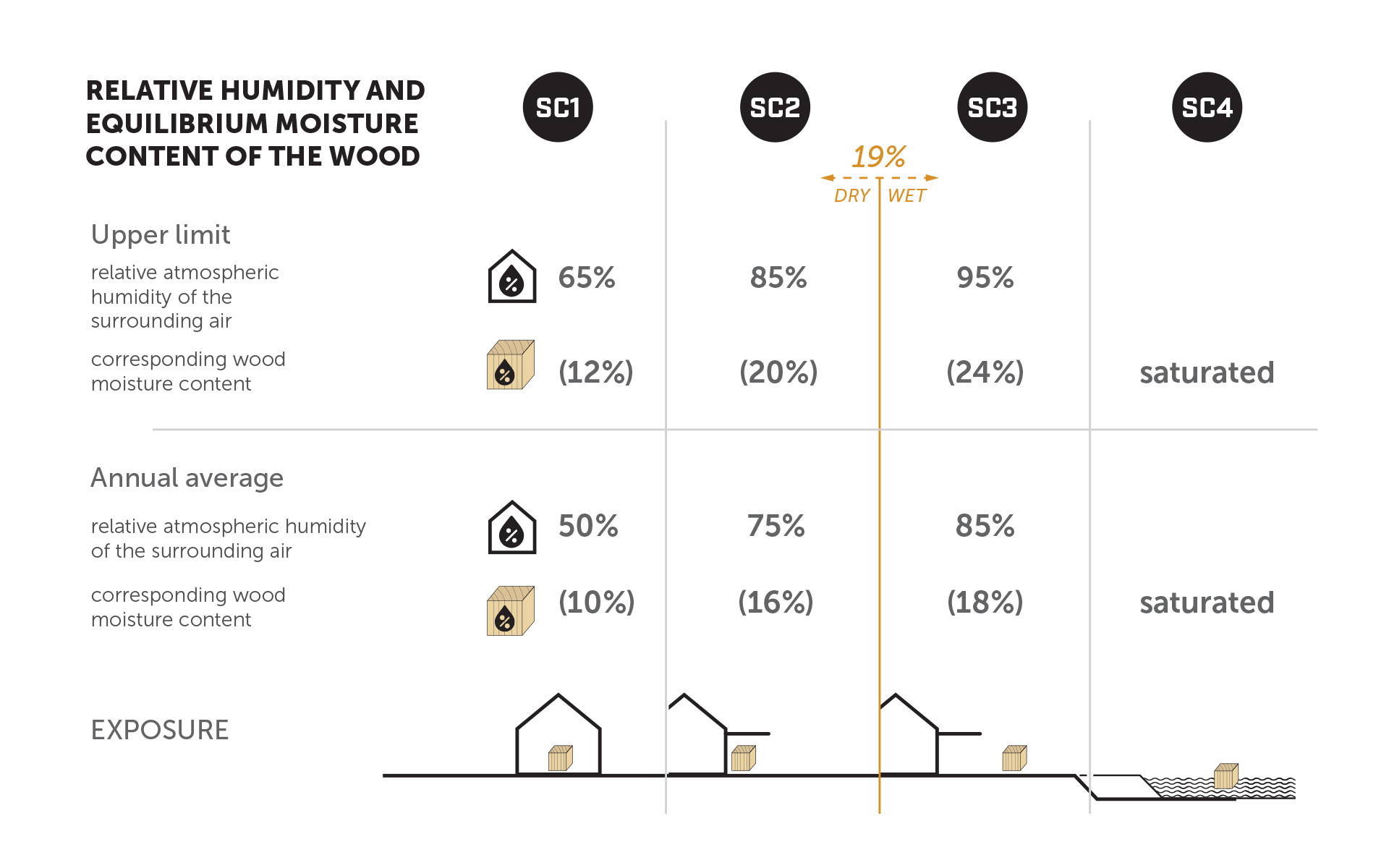
Atmosphärische Korrosivitätskategorie
Die Norm EN ISO 9223 unterteilt die atmosphärische Korrosivität in fünf Kategorien, von C1 (sehr niedrig) bis C5 (sehr hoch). Diese Kategorien berücksichtigen:
Luftverschmutzung: Vorhandensein von Schadstoffen in der Luft (z. B. Schwefeldioxid oder Chloride).
Luftfeuchtigkeit: Häufigkeit und Dauer von Phänomenen wie Regen, Nebel und Kondensation.
Eine C5-Umgebung ist beispielsweise typisch für Küstenorte oder in der Nähe von Schwerindustrie, wo Salz und chemische Dämpfe die Korrosion von Holzbauschrauben beschleunigen. In einer C1-Situation, beispielsweise einem gut geschützten Innenraum, sind die Korrosionsrisiken minimal, und es können Schrauben mit dünneren Beschichtungen verwendet werden.
Korrosivitätskategorien des Holzes
Die Norm EN 14592:2022 unterteilt die Korrosivität von Holz ebenfalls in fünf Kategorien, von T1 (sehr niedrig) bis T5 (sehr hoch).
Die Korrosivitätskategorie des Holzes ist abhängig von:
Säuregehalt und Holzart: Je nach Holzart ist ein mehr oder weniger hoher Anteil an Essigsäure vorhanden, die eine korrosive Wirkung auf die enthaltenen Metalle hat. Die Menge dieser Säure bestimmt den pH-Wert der Holzart. Je niedriger der pH-Wert, desto aggressiver die Holzart.
Chemische und Wärmebehandlungen: Imprägnierung, Flammschutzmittel, Kupfersalze oder Chloride verändern die Reaktivität des Holzes bei Kontakt mit Metall.
Feuchtigkeitsgehalt im Holz: Ein hoher Feuchtigkeitsgehalt begünstigt die Ausbreitung korrosiver Stoffe bis zur Oberfläche der Schraube sowie die elektrochemische Reaktion, die während der Korrosionen erfolgt.
Praktisch bietet die umfassende Bewertung der Nutzungsklassen, atmosphärischen Korrosionskategorien und der Korrosionskategorie des Holzes Aufschluss über die Bedingungen, denen Holzschrauben unterzogen werden.
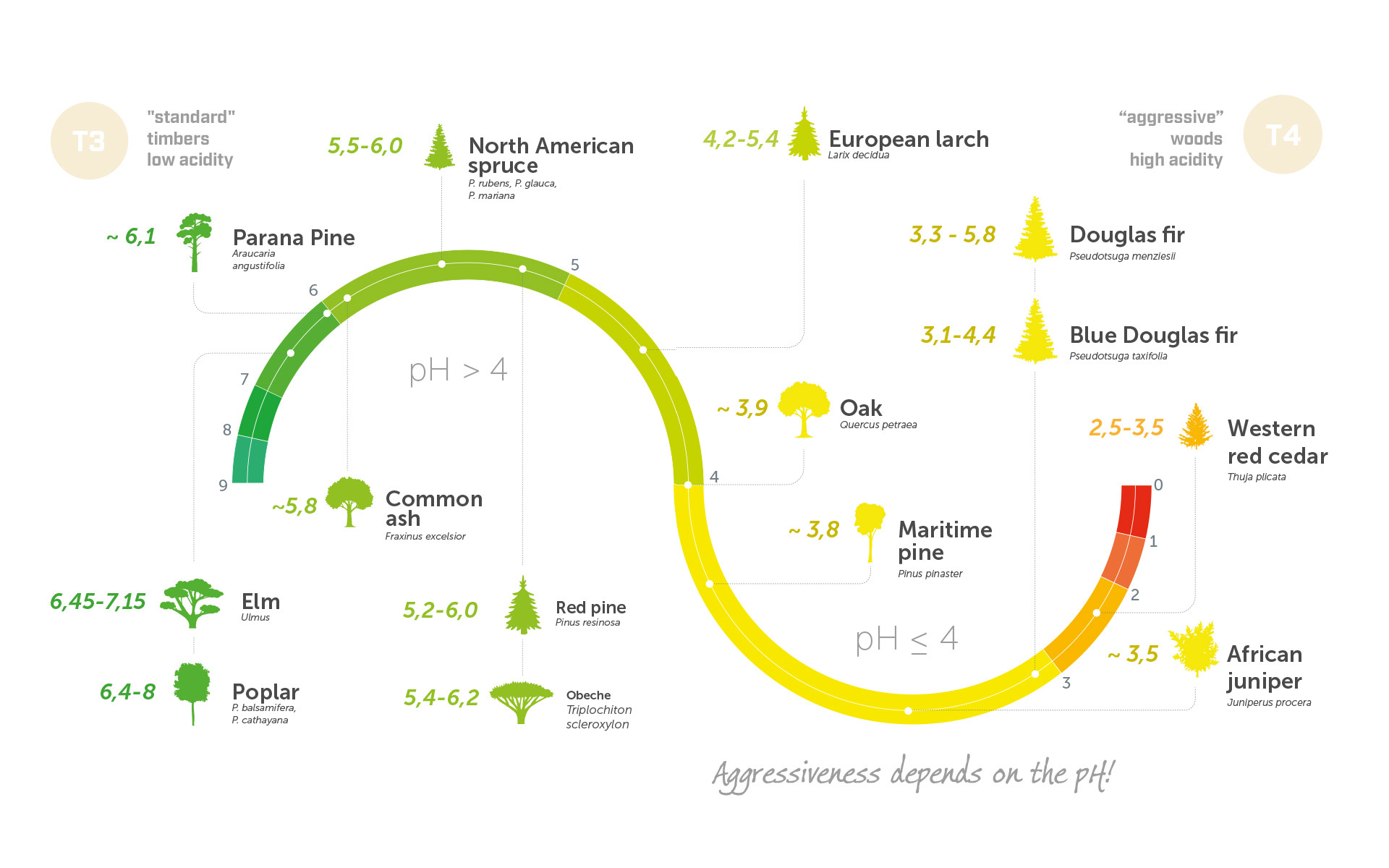
Holzarten, Tannine und pH-Wert: bei der Wahl der Holzbauschrauben zu berücksichtigende Aspekte
Nicht alle Hölzer reagieren in gleicher Weise auf Metall. Einige Arten, wie die Eiche, weisen einen hohen Gehalt an Tanninen auf – Stoffe, die eine schützende Patina auf der Schraube bilden können. Bei Holzarten mit einem besonders sauren pH-Wert (unter 4) oder in feuchten Umgebungen kann jedoch die Eiche selbst korrosive Reaktionen fördern. Hier zwei Beispiele:
Eiche:
Sehr tanninhaltig, wodurch die Korrosionsgeschwindigkeit lokal reduziert werden kann.
Bei hoher Luftfeuchtigkeit (SC3 oder WET) kann ihr Säuregehalt die Korrosion beschleunigen.
Tanne:
Geringer Tanningehalt.
Weniger aggressiv in Bezug auf den pH-Wert und somit sehr viel weniger aggressiv in feuchten Umgebungen.
Zwar werden in der Regel Tannine mit Korrosionen in Verbindung gebracht, da viele tanninreiche Hölzer auch sauer sind (pH < 4), aber der wichtigste Faktor, den es beim Korrosionsprozess im Holz zu berücksichtigen gilt, ist die Korrosivitätskategorie (T), die mit dem pH und der Feuchtigkeit im Zusammenhang steht.
Die Beurteilung der Holzart, ihres pH-Werts und der möglichen Behandlung (mit Chloriden oder Kupfersalzen) ist daher ein entscheidender Schritt bei der Auswahl von Holzbauschrauben. In sehr sauren Umgebungen können hoch korrosionsbeständige Edelstähle (wie AISI 316) die zuverlässigste Lösung sein.
Was geschieht mit Holzbauschrauben in den verschiedenen korrosiven Umgebungen? Eine Versuchskampagne
Eine konkrete Möglichkeit, die Umgebungsauswirkungen auf die Korrosion zu verstehen, sind Tests im Maßstab 1:1. Im Forschungs- und Entwicklungslabor fand eine Versuchskampagne mit etwa 350 Konfigurationen von Holzbauschrauben statt, die für ein Jahr unterschiedlichen Bedingungen ausgesetzt waren.
Aufbau des Experiments
Geprüfte Materialien: 6 Arten von Schrauben, aus einfachem verzinktem Kohlenstoffstahl bis zu verschiedenen Edelstahlsorten.
Bedingungen:
Holz: Eiche
Nutzungsklasse: SC3
Atmosphärische Korrosivitätskategorie: C2 (geringe, aber nicht vernachlässigbare Aggressivität).
Korrosivitätskategorie des Holzes: T4 (hohe Korrosionsneigung aufgrund des Säuregehalts des Holzes).
Ergebnisse
Nach 1 Monat:
Die galvanisch verzinkten Schrauben zeigen erste Anzeichen von Tanninen an der Oberfläche, insbesondere am Gewinde.
Die Schrauben aus Edelstahl (AISI 410) zeigen keine Anzeichen von Oxidation.
Nach 10 Monaten:
Die galvanisch verzinkten Schrauben zeigen offensichtliche Anzeichen von rotem Oberflächenrost.
Die Schrauben aus Edelstahl (AISI 410) zeigen Anzeichen von Tanninen, aber keinen Rost.
Dieser Test belegt, wie entscheidend die Montagebedingungen und die Holzart sind. Selbst eine für eine bestimmte Exposition ausgelegte Beschichtung reicht möglicherweise nicht aus, wenn die Gesamtkorrosivität (Atmosphäre und Holzmerkmale) über dem vorgesehenen Wert liegt.
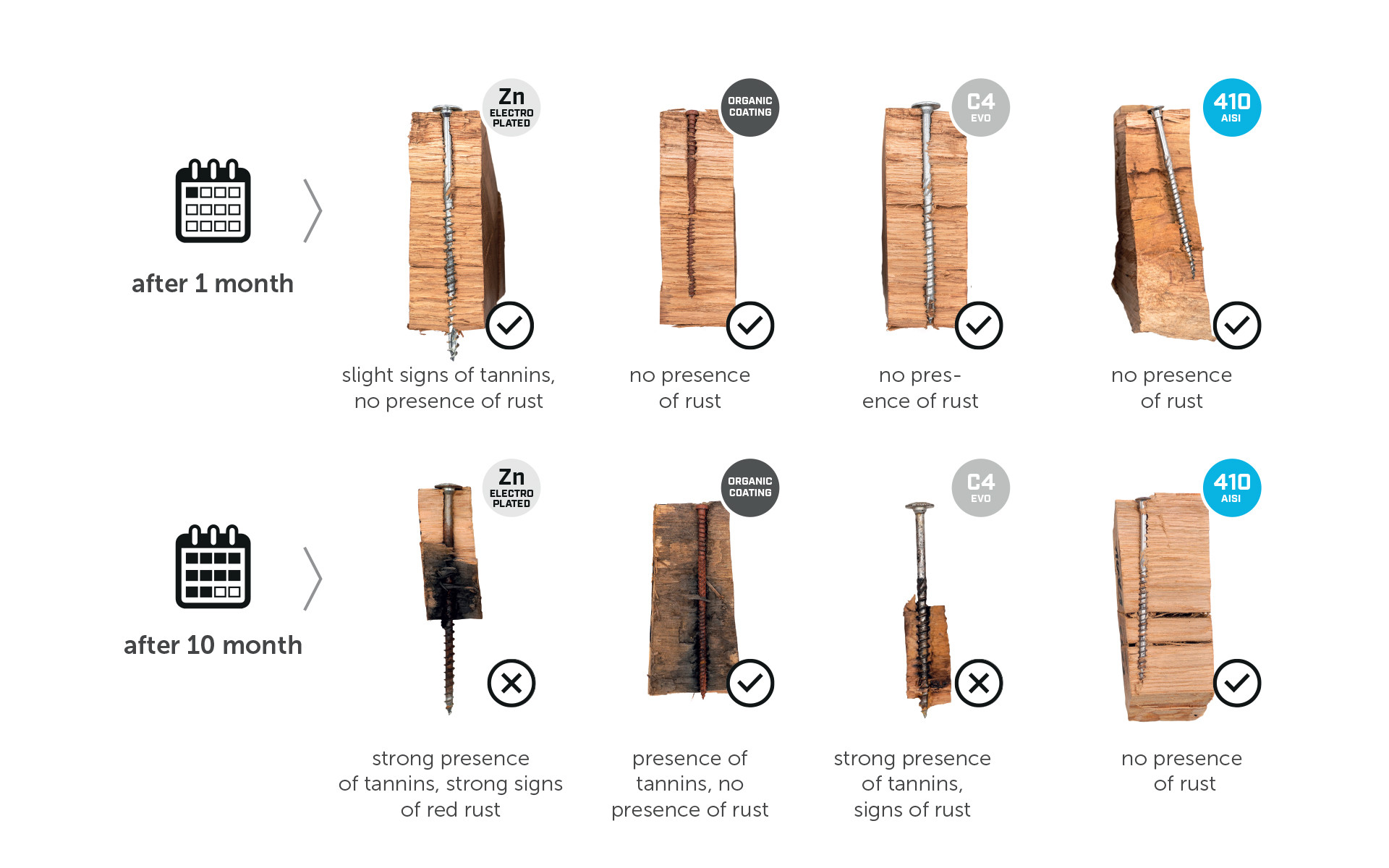
Stahl und Beschichtungen von Holzbauschrauben: die richtige Lösung
Kenner der Baubranche wissen, dass es keine universelle Schraube gibt. Jede Situation erfordert spezifische Werkstoffe und Beschichtungen. Im Allgemeinen unterteilen sich Holzbauschrauben in zwei große Familien: Kohlenstoffstahl mit Beschichtung (Verzinkung oder fortschrittliche Behandlungen) und Edelstahl.
Kohlenstoffstähle mit Beschichtung:
Oftmals die wirtschaftlichste Lösung mit hoher mechanischer Leistung.
Abhängig von der Art der Beschichtung bieten sie unterschiedlichen Schutz: von der einfachen elektrolytischen Verzinkung bis hin zum C4 EVO oder C5 EVO Coating speziell für sehr aggressive Umgebungen. Die Beschichtung C4 EVO wurde für hohe Leistungen bei aggressiven Witterungsbedingungen entwickelt. Bei aggressiven Holzverhältnissen ist Edelstahl die richtige Wahl.
Hierbei ist eine detaillierte Analyse der tatsächlichen Bedingungen erforderlich, da sie in feuchten und schadstoffreichen Umgebungen korrodieren können.
Edelstähle:
HCR: Garantiert die höchste Korrosionsbeständigkeit auch in Gegenwart von Chloriden und Schadstoffen. Es handelt sich um die beste Wahl in extremen Fällen, wie beispielsweise bei Hallenbädern.
AISI 316 (A4): Empfohlen in Meeres- oder Industrieumgebungen, in denen die Schraube Salzen, Schadstoffen und aggressivsten Hölzern (T5) ausgesetzt ist.
AISI 304 (A2): Kostengünstigere Alternative für schwierige Bedingungen, jedoch weniger anspruchsvoll als die oben genannten. Hohe Beständigkeit gegen saure Hölzer (T4).
AISI 410: Martensitischer Stahl mit guten mechanischen Eigenschaften und moderater Korrosionsbeständigkeit (fern von Chloridquellen); ideal für einen Kompromiss zwischen Robustheit und Haltbarkeit. Vorabtests zeigen eine gute Festigkeit in sauren Hölzern (T4).
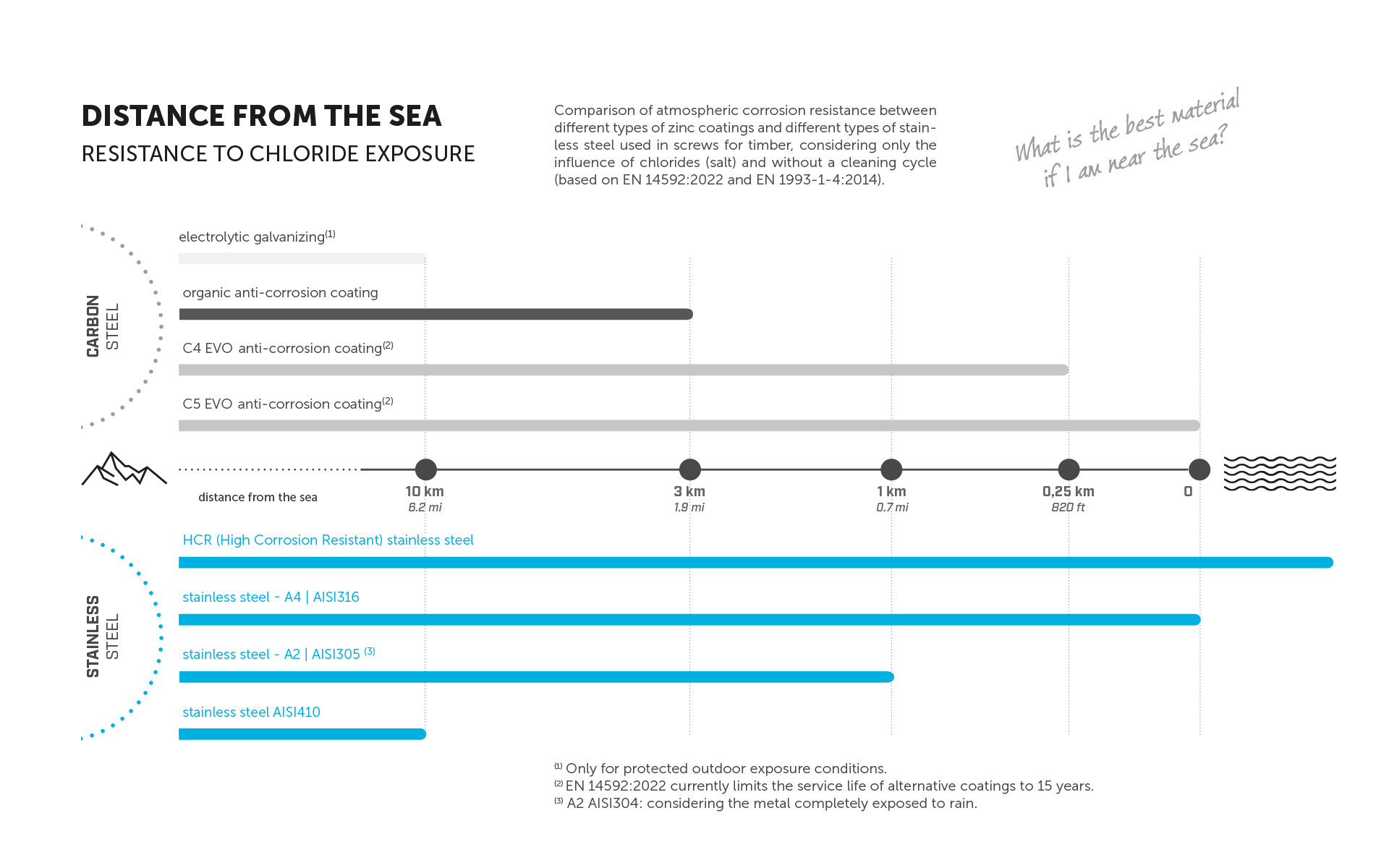
Rothoblaas-Diagramm für die Wahl der Beschichtung und entsprechender Videokurs: zwei unverzichtbare Tools.
Da es verschiedenste Einflussfaktoren und zahlreiche Variablen zu berücksichtigen gilt, die in der Lage sind, korrosive Prozesse auszulösen oder zu verstärken, haben wir in einem gut verständlichen Diagramm die Bewertung des Korrosionsschutzverhaltens von Materialien und Beschichtungen abhängig von der Korrosivitätskategorie der Umgebung und der Korrosivitätskategorie des Holzes zusammengefasst (gemäß EN 14592:2022 und EN 1993-1-4:2014). Dieses Diagramm ist hier und im Smartbook Schrauben zu finden
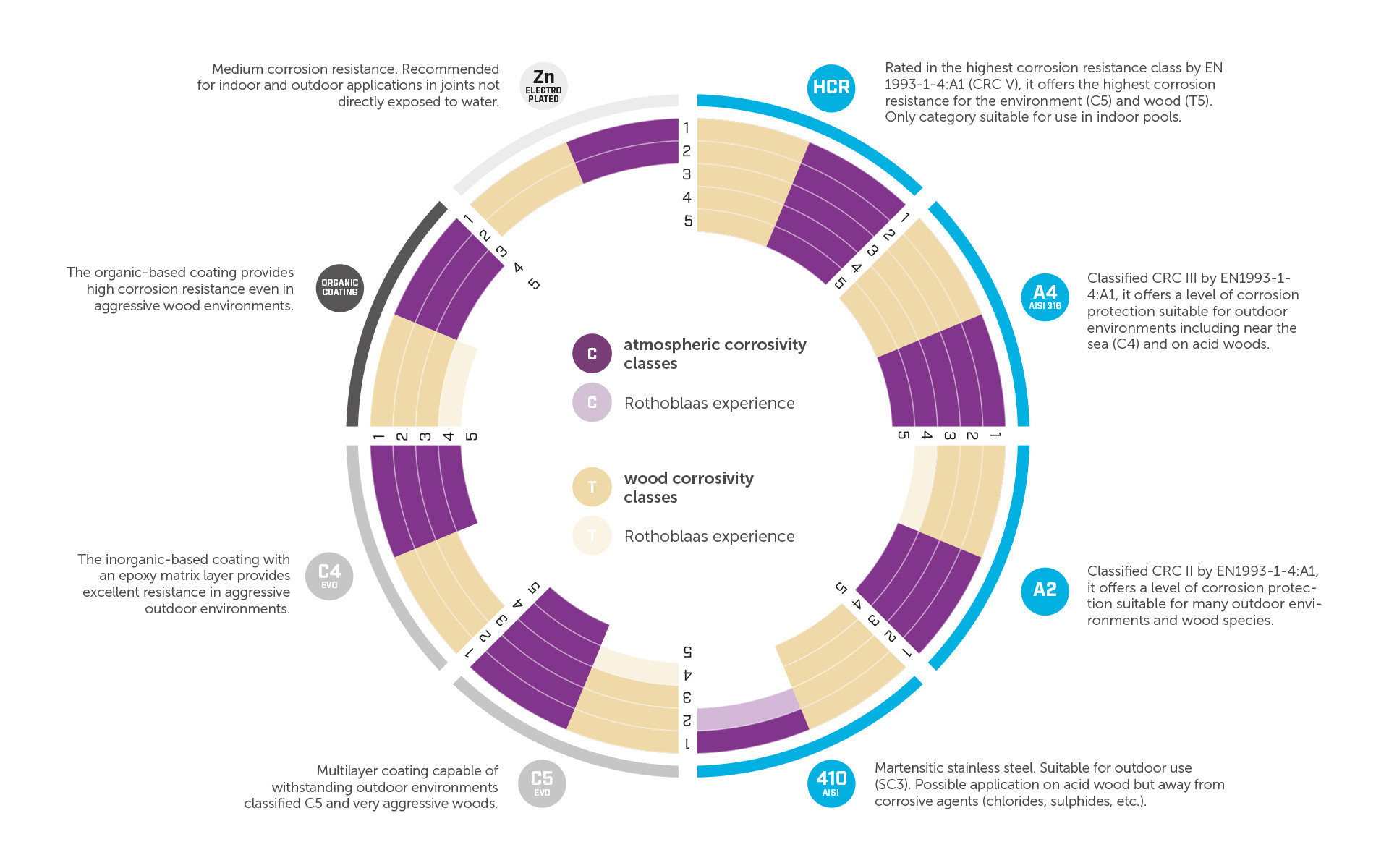
Die Komplexität des Themas stellt uns vor zwei Verpflichtungen: einerseits unsere Produkte konstant zu prüfen und weiterhin in Forschung und Entwicklung zu investieren, um noch leistungsfähigere Lösungen anbieten zu können, und andererseits den Branchenprofis alle notwendigen Instrumente zur Hand zu geben, um sich ein genaues Bild davon zu machen, wie und wann Rothoblaas-Schrauben verwendet werden.
Aus diesem Grund haben wir ebenfalls eine Videolektion erstellt. Sie bietet vertiefende Einblicke zu einigen in diesem Artikel behandelten Themen wie auch eine Reihe weiterer Anregungen und Daten zum besseren Verständnis.
Alle Rechte vorbehalten
Technische Details
- Jahr:
- 2025
- Land:
- Any
- Produkte:
- HBS EVO VGS EVO HBS VGZ EVO SHS SHS AISI410 HBS HARDWOOD TBS EVO TBS VGZ VGS KKT A4 | AISI316 KKF AISI410 HBS PLATE A4 HBS PLATE EVO HBS PLATE KKA AISI410 HBS EVO C5 SCI HCR